CLASH DETECTION – PREVENTING CONSTRUCTION ISSUES
“You can use an eraser on the drafting table or a sledgehammer on the construction site.”
These words were spoken by none other than Frank Lloyd Wright, and while the tools of the trade may have changed, the sentiment has never been truer.
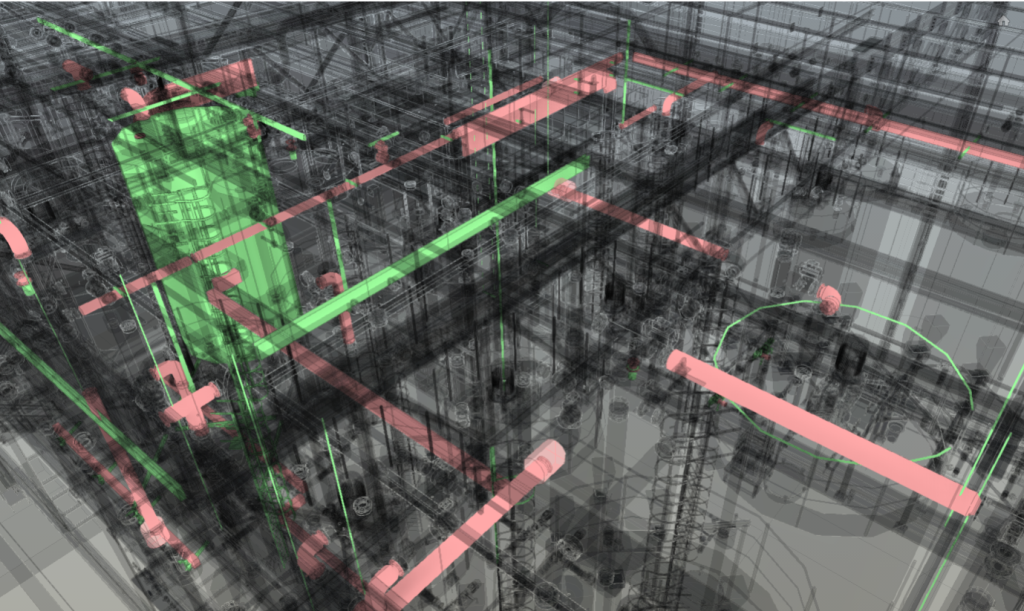
The modern eraser for any complex build is a process known as clash detection. Before components are ordered, delivered, or prefabricated, a digital representation of those components is combined in a virtual 3D environment and compared. The software can quickly point out where one component collides with another. Examples include a drainpipe running through a foundation footing, a sprinkler head in conflict with a duct, or light switches buried inside a column.
Due to the rigid necessity of many architectural and structural elements in a design, it is not uncommon for contractors and others to refer to clash detection as MEP coordination. The operative assumption is that various mechanical, electrical, and plumbing components must be adjusted and routed around conflicts.
Ultimately, all the hard clashes are resolved. The only question is whether clashes are addressed through updates to virtual models and drawings or in the field. Working through clashes in the design phase is more efficient and cost-effective than on the construction site.
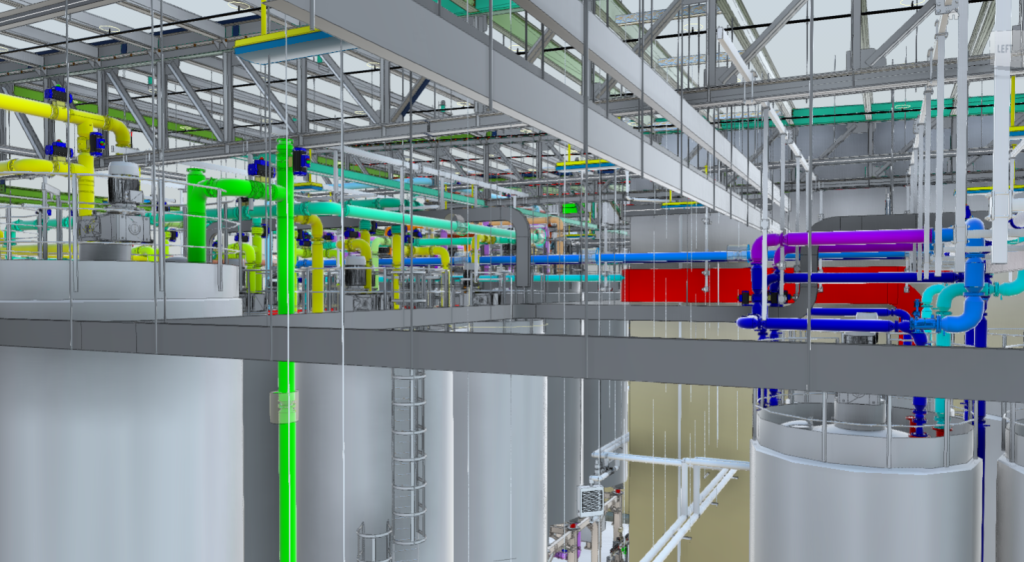
In his book, The Checklist Manifesto, Dr. Atul Gawande visited an active construction project and marveled at using a software application he referred to only as the ‘Clash Detective.’ The sobering message for the AEC industry is that we were presumed ahead of other industries (such as healthcare) in applying our knowledge to work through every possible conflict. It seems clear that in 2022 and beyond, building projects that skip design review through clash detection exercises are not meeting the standard of care for our industry.
Many potential issues go beyond a software’s current identification capabilities, so involving field personnel in the review of models is always a good idea. The experience gained on one project leads to checking for the same challenges on future projects.
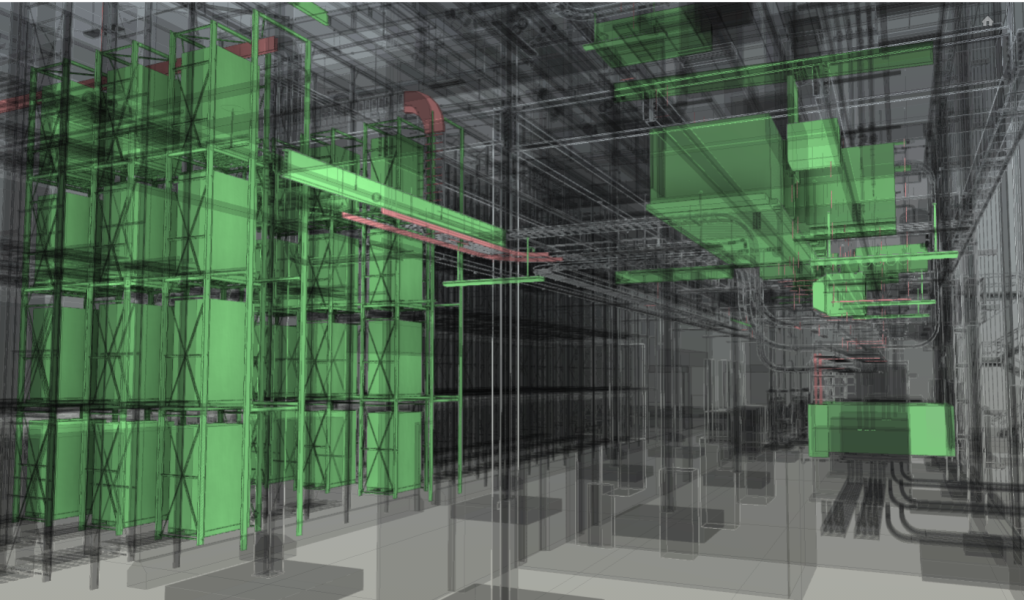
Case in Point
Building professionals should understand early in the design process about connection points for building services. Somewhere between all the code books and the operations manuals, there are some practical minimums for equipment clearances. Only veteran modelers are savvy enough to show such clearance zones within the computer’s representations. And often, those who have worked in the field have insights into where following the manual or meeting the minimum code requirement isn’t going to provide the best result.
There is not, in fact, a computer application called clash detective. Until recently, this model-checking feature was only found in a single software tool. One of the most powerful changes in the methodology was when it became possible to identify conflicts and share the exact 3D viewpoint (and notes for resolution) with the modeler in their authoring application.
Prior to this change, it was necessary to hold clash review meetings so everyone could crowd in together to see the issues for the first time. Now tracking issues and sharing them can occur within minutes of identification. We can keep the topical dialogue outside of regularly scheduled meetings. Instead of walking into a model review meeting and not knowing what issues will be raised or that you’ll be tasked to fix, team members can turn to assignments on the tracked issues list.
Meetings can then be used to check and confirm that things have been (or soon will be) resolved. We can delve deeper into an issue, increasing both awareness and the possibility that someone else on the team may have a better idea of how to resolve the conflict.
Another change seems to be in the air. While clash detection was once a discrete activity with the potential of not applying the coordination of models to the building process, it is now feasible to manage the 3D model changes, field reports, and digital images in one unified platform. Knowing that the same models can serve both aspects of quality assurance helps us to deliver our customer’s projects on time and with a minimum of re-work.
Thank you to Nirav Mehta, Mark Osborne, and Brian Zuzik for contributing to this blog post.
![]() |
ANDREW FISHERBIM ManagerCall 949.451.9913 | Email Andrew | View Profile |