Superflat Floors: Design and Construction Considerations for Industrial Settings
In this age of advanced machinery, robotics, and complex logistics systems, superflat floors are critically important to operations. Superflat floors can:
-
- Determine the kind of racks and logistics systems to be utilized in the operation.
-
- Impact the amount of maintenance needed on equipment.
-
- Be used for advanced robotics and rapid picking systems.
-
- Impact how fast fork trucks, robotics, and other equipment can move around the facility.
-
- Minimize risk of rack impacts and handling errors.
-
- Improve the safety of the operations.
Installing superflat floors allows for taller storage systems and, potentially, tighter aisles, faster operations, less maintenance costs, and, oftentimes, a safer operating setting. All are desirable benefits for industrial plant and facility owners.
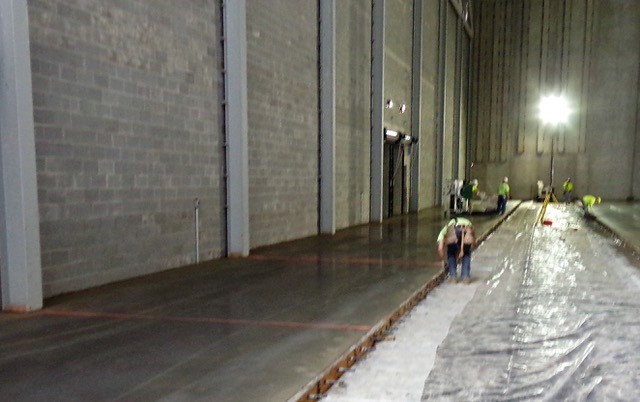
Considerations
-
- Understand equipment manufacturer’s floor flatness and levelness requirements related to performance. It is critical to understand the exact requirements and reasons for the guidelines versus making assumptions like using past reference points.
-
- Coordinate the structural engineer or floor designer and the geotechnical engineer to agree upon soil loading and settlement requirements. This is critical for determining which soil improvement system will be recommended.
-
- Base design details for the floors, including thickness, reinforcing, joint spacing, and layout on the superimposed loading criteria and geotechnical recommendations. Superflat floors must meet the demands of heavy wheel traffic, often in specific lanes in narrow aisles. The concrete floor surface must be hard, wear-resistant, and not create concrete dust. Careful specification of the concrete materials, proper finishing techniques, and surface treatments such as liquid hardeners are proven methods of ensuring wear-resistant slabs.
-
- Coordinate and partner field operations and engineering team for size and layout of planned concrete floor placements.
-
- Conduct an in-depth preconstruction conference involving the structural engineer, concrete supplier, concrete finisher crew, concrete testing lab, and geotechnical engineer.
-
- Utilize specialized construction equipment, including laser screed machines and adjustable side forms set with laser levels.
-
- Place superflat floors under a roof to control sun and wind. Both can cause the uneven setting of the concrete, which will result in flatness issues.
-
- Provide proper lighting during finishing operations for the concrete workers.
-
- Hire adequate numbers of experienced workers to place and finish the slab uniformly. Uniform timing promotes even curing and flat floors.
-
- During installation, ensure joint saw-cutting, curing, and testing is per concrete specifications.
-
- Have engineers review reports such as concrete compressive test reports, flatness reports, and levelness reports. Don’t just review them in the field or receive and file them without review.
-
- Understand current industry standards which define the measurement of a floor flatness within 48 hours of placement. However, concrete shrinkage and curling continue for several months after placement and can cause changes to the floor slab reducing the slab flatness.
-
- Control cracking. Concrete slabs, including superflat slabs, are subject to cracks. Crack control of super flat slabs begins with an awareness of the considerations listed above. This includes proper concrete mix, proper joint spacing, careful detailing to avoid restraint of slab components, finishing equipment, finishing procedures, and curing. Additional techniques used to control cracking in superflat slabs include post-tensioning, shrinkage compensating concrete and admixtures, over-reinforced slabs, and distributed synthetic reinforcement.
Did You Know?
Austin has been designing and constructing floor systems to tight flatness and levelness specifications since the 1950s. However, it wasn’t until the 1970s that industrial and warehouse owners started increasing the density of their storage configurations to minimize investments in land and facilities to optimize operations.
In 1987, Barry Rogers, PE, Senior Project Manager and Project Executive with Austin’s Research and
Development department, patented one of the first formal measuring devices for floor flatness allowing for a scientific method of testing and laser measuring these special floor systems.
In 2017, and our partners set the world record for floor flatness and levelness design and construction.